Decision making is an important activity at the centre of every industrial processing plant. Whether itās deciding on how to optimise manufacturing efficiencies in the face of supply chain fragility, or how many engineers to safely deploy in the field to maintain operations 24/7. It all helps to power efficiencies, compliance, sustainability and competitiveness, explains Intowareās CEO Keith Tilley.
According to the Made UK/PWC Executive Survey 2022, UK manufacturers felt positive about growth in the beginning of this year having survived the pandemic. This is despite the fact that processing plants face a number of threats. These threats include supply chain disruption, labour shortages and rising material costs. Since then, Russiaās invasion of Ukraine has caused energy prices to surge, impacting heavy industries. Disconnected data often exacerbates these issues.
In the face of these challenges, being able to respond quickly and accurately is critical not only to competitiveness, but survival. Having an effective digital strategy in place that delivers actionable insights is the key to mitigating many of these issues. Particularly, that of disconnected data.
Embracing technology
Industry 4.0 and the Industrial Internet of Things (IIoT) technology, facilitates the access to data in āreal-timeā. This occurs without the need to take the assets being monitored out of service. Thus, allowing access to critical data that supports asset managers, supervisors and frontline workers. Consequently, corrective action can be taken to minimise downtime and ensure production targets and compliance standards are met.
To better understand how data informed businesses are post-pandemic, workflow automation specialist Intoware commissioned an independent survey of 1,030 decision-making industrial businesses. This took place on the 28th February to the March 2022.
It included manufacturing, utilities, oil and gas, civil engineering and rail transport and logistics sectors. Everyone from senior decisions makers, managers, supervisors to frontline workers were asked key questions to discover how they use data. Their attitudes towards data for business decision making were also explored.
Survey findings
Intoware found that 74% of manufacturers post-pandemic, are relying on legacy systems and spreadsheets to get tasks done. They believe this inflexible, often out-of-date, disconnected data is sufficient to support corporate decision making.
The survey showed that most manufacturers, 86%, claimed to be data-informed and 76% trusted data enough to complete tasks. This is despite most of them still relying on disparate legacy systems. Disconnected data is a common issue that needs addressing.
Intowareās CEO, Keith Tilley, comments: āThe research revealed that most of those surveyed believe they are data-driven. In reality, they could be relying on old, out-of-date data. This disconnected data acts like a ball and chain, tying down your staff. They spend a huge amount of time trying to unlock data trapped in spreadsheets and legacy systems to meet the demands of businesses, customers and regulators.ā
With 77% of decision makers having access to data and over three quarters, 82%, believe that data is an asset. This is very good news. However, just under half of those surveyed, 47%, use data only occasionally to help get the job done. The reality is that their data is siloed.
While over half of those surveyed, 64% are interested in using digital software ātoolsā to support their role. It seems that a significant minority simply donāt have the skills to use the new data these systems provide. 21% feel overwhelmed and another 24% feel only slightly confident when using data to back decision making. That is almost half, 45% of those surveyed.
Despite this, when it comes to passing on critical skills and expertise from ageing workers to help plug the skills āgapā for the next generation, 74% see digital ātoolsā as playing a valuable part in sharing knowledge. So, itās no surprise that over half of companies, 60% intend to invest in data skills, training and development in 2022 to help meet this challenge.
A culture of un-informed decision-making
While it seems that a culture of un-informed decision making still persists for many, with 26% having made decisions based on āgut-feelā during their careers. Over a third, 21%, do this on a monthly basis and a worrying 16% each week.
This culture goes right to the very top of businesses. Just under a third, 28%, of senior decision makers and 27% of managers rely on āgut-feelā. This can have serious implications. For example, when managers need to introduce engineering changes without assessing the impact on current works, which is detrimental to business performance.
So why isnāt it yet working, with most businesses relying on siloed data that risks flawed decision making and low productivity? A simple answer to this challenge lies with smart digital workflow technology. Intoware developed its digital work-instruction platform WorkfloPlus using mobile and assisted reality (AR) wearable devices from RealWear. Disconnected data is a severe obstacle in fully leveraging these technologies.
WorkfloPlus converts out-of-date paper-based and legacy processes into easy to follow, step-by-step digital work-instructions. It gives frontline engineers access to the data resources, information and support they need to complete critical procedures. Most importantly, it provides the data analytics needed to help streamline asset maintenance and compliance, delivering a proven 200% gain in productivity.
Manufacturer Bayer Pharmaceuticals digitises batch change-overs
A forward-thinking client, Bayer Pharmaceuticals is deploying WorkfloPlus combined with RealWear āhands-freeā AR headsets. The goal is to streamline and manage its critical production change over process and improve accuracy, in what is a highly regulated market.
Drug manufacturing operations require regular cleaning and change overs between each batch. By using digital work-instruction platform WorkfloPlus it allows this procedure to be taken in a constant and timely manner, to help minimise ādown-timeā for greater cost efficiency. At the same time, it provides thorough audit checks that satisfy rigorous GxP (good practice) compliance standards, preventing the risk of fines – better than any paper ātick-listā could deliver.
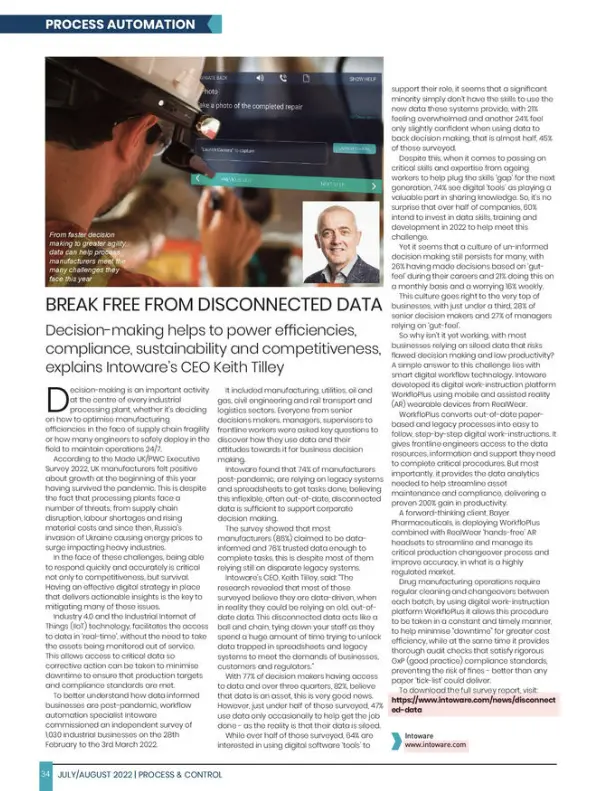
Download our Why is Disconnected Data Holding You Back? whitepaper to find out how you can break free from disconnected data.