How did you get started in the industry?
A long time ago!! I had an early interest in technology that led me into starting out in computer operations for an automotive company.
From there I moved into a business development role, where using the latest technology to help companies to improve their business outcome was key to success.
This has allowed me to see how different technology best practices can be transferred between industries. This is particularly true in the rail industry where it has such a wide use, from “front of house” with travellers to behind the scenes track inspections, maintenance work and ensuring health and safety, and compliance.
How has technology developed since you started in the industry?
The rail industry has been transformed by technology in various ways and has played a crucial role in helping to make it safer, more efficient, and more environmentally sustainable. It has also, despite some headlines to the contrary, greatly enhanced the passenger experience.
Technology has driven improvements to the infrastructure, as well as the trains themselves, thanks to a wide range of areas such as Digitalisation, Automation, Communication, Information Systems and Safety. These developments have helped to develop predictive maintenance algorithms, advanced communication systems (including Wi-Fi on trains), real-time monitoring systems, and safety enhancements.
Tell us about Intoware
Intoware is a Nottingham based SaaS company specialising in the development of mobile workforce management solutions. Our flag ship product, WorkfloPlus, is key to help companies start on their digital transformation journey.
Our aim is to partner with our customers to ensure successful delivery and deployment of a project, so they get the maximum return from their investment as soon as possible, which we do this through a simple Engage – Design – Deploy methodology to ensure the desired business driven outcomes are achieved.
What types of products and services do you offer?
Our digital work instruction platform, WorkfloPlus, streamlines operations, improves productivity, and enhances worker safety by digitalising procedures and optimising processes. It can either make use of the mobile technology that workers are familiar with or run on the latest wearable technology to make use of innovative features such as AR/AI if hands free working is needed. It maximises the efficiency and safety of the workforce and adapts to the demands of modern industrial environments to drive operational excellence.
How have the products and services you offer developed over the years?
Intoware was born in 2015 and since then we have developed and enhanced WorkfloPlus to meet the changing needs of our customers and the market. As well as running on iOS, Android, Windows and wearable devices, we’ve also ensured it can be integrated into existing ERP systems to generate a 100% real-time accurate view of your frontline operations.
The instant digital report removes the time previously wasted by inputting information from paperwork. It also eliminates any data-lag which means repairs can be scheduled quicker than ever before.
We have also enhanced WorkfloPlus’ team management capabilities so larger jobs can be split into individual tasks and assigned to the most qualified person to compete that process. However, there’s also the possibility of connecting to a remote expert if a more experienced workers input is needed to complete the task at any point, rather than having to reschedule the whole job.
The increased use of technology has definitely accelerated over years. We have even incorporated digital workflows into the use of drone technology, so workers could keep their feet on the track rather than increase the safety risk by working at height when carrying out maintenance inspections.
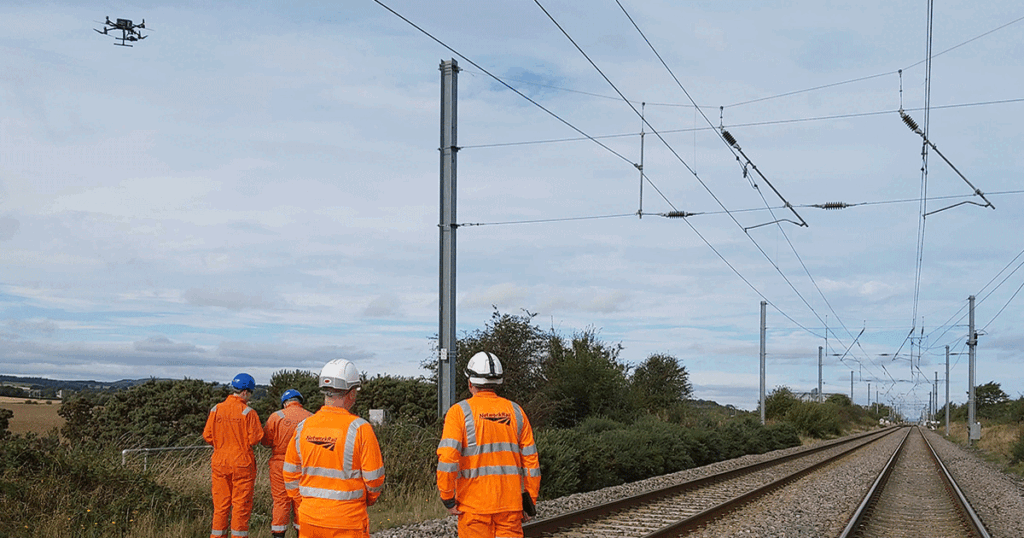
How can the industry tackle its skills shortage and how do you recruit/retain/train your staff?
WorkfloPlus is a key tool to help tackle the current skills shortage crisis through its training and upskilling capabilities. By digitalising the knowledge from experienced workers it’s possible to retain and store their best practices for future generations.
This means workflows can be designed and enhanced that can educate and train the next generate, which really helps to enable a new work force to quickly come up to speed. Combined with the remote expert communication, you can provide over the shoulder support to maximise the use of the experience staff in assisting trainees.
Have you changed your approach to work at all since covid?
Since Covid Intoware has moved towards a more hybrid and flexible way of working. We still have our headquarters in Nottingham, but by moving to a hybrid and remote model of working we’ve been able attract and retain the right staff to enhance our product and services from further afield too.
In terms of technology, how do you anticipate things might change in the next five to ten years?
Technology changes very rapidly, no sooner do you think you know it then it changes again. This is why it is exciting to work in the industry and to see how it can future benefit business and individuals.
Clearly over the next 5-10 years, AI (Artificial Intelligence) and AR (Augmented Reality) are likely to have profound effects across various industries, driving significant changes in the way we work, interact with technology, and experience the world. Whether this be: enhanced Productivity and Efficiency, Personalised Experiences, Improved Communications, AI and AR will likely empower the connected worker.
AI and AR hold tremendous potential to transform the rail industry further and help with its digital transformation journey.
What are the key benefits of the products and services you offer to the Rail Industry?
The key benefits of WorkfloPlus from Intoware are:
- Efficiency: WorkfloPlus can streamline workflows and processes within the rail industry, reducing manual tasks and administrative overhead. This efficiency improvement leads to faster turnaround times, optimised resource allocation, and ultimately cost savings.
- Compliance Management: WorkfloPlus helps ensure compliance with industry regulations and safety standards by providing tools for tracking and managing regulatory requirements, certifications, and inspections. This reduces the risk of non-compliance penalties and improves overall safety and reliability.
- Asset Management: The platform enables comprehensive asset management, allowing rail companies to track the status, maintenance history, and performance of their infrastructure, rolling stock, and equipment. This proactive approach to asset management minimizes downtime, extends asset lifespan, and enhances operational reliability.
- Resource Planning: WorkfloPlus facilitates effective resource planning by providing insights into workforce availability, skills, and schedules. This enables rail operators to allocate resources efficiently, minimise idle time, and optimise workforce productivity.
- Data Analytics: The platform offers advanced analytics capabilities, allowing rail companies to analyse operational data, identify trends, and make data-driven decisions. This insight enables continuous improvement initiatives, enhances operational efficiency, and supports strategic planning.
- Collaboration and Communication: WorkfloPlus fosters collaboration and communication among various stakeholders within the rail industry, including maintenance crews, dispatchers, and management teams. This improves coordination, reduces misunderstandings, and enhances overall organisational effectiveness.
- Mobile Accessibility: WorkfloPlus is accessible via mobile devices, enabling field workers to access critical information, submit reports, and communicate in real-time while on the go. This mobility improves responsiveness, enables faster decision-making, and enhances operational agility.
- Scalability and Customisation: The platform is scalable and customisable to meet the specific needs and requirements of different rail operators. Whether managing a small rail network or a large-scale transportation system, WorkfloPlus can be tailored to accommodate varying levels of complexity and operational demands.
Overall, WorkfloPlus can provide rail companies with a comprehensive solution for optimising their operations, improving safety and compliance, and driving efficiency gains across the organisation.
Contact us to find out how WorkfloPlus can help the Rail industry on it’s digital transformation journey.