Rimstock is Britain’s leading alloy wheel manufacturer, it designs, manufacturers and supplies to some of the world’s most prestigious auto marques including Lotus, Alpina, BMW and McLaren. Based in West Bromwich its engineering plant specialises in the advanced manufacturing of forged and cast aluminium wheels for OEM’s, motorsport, defence, concept and aftermarket sectors.
The automotive market has been challenging recently for Rimstock, Brexit and the resulting economic uncertainty and increasing emissions targets meant the need to stay competitive through innovative design and unrivalled service was ever present. The manufacturer responded by beginning its digitalisation journey to help streamline quality inspection audits beginning with its state-of-the-art paint facility.
Having recently joined Rimstock as its new Operations Manager, Mike Wise knew that the manual paper-based approach to inspection audits and compliance that the manufacturer relied on was in need of urgent review.
Returns and the associated costs had been escalating, creating added pressure since each returned alloy wheel had to either be reworked or manufactured incurring further costs. This was all a major concern for a manufacturer whose reputation depends on delivering the very highest quality.
The first step on the digitalisation journey
Having spearheaded digitalisation projects in a previous role where he introduced WorkfloPlus from Intoware to enable the business to go paperless. Mike aimed to use this digital ’tool’ once again to improve Rimstock’s inspection and compliance audits and prove beyond doubt its products are always defect free when they leave the plant.
WorkfloPlus would also provide the quantifiable data needed for Rimstock’s failure mode effects analysis (FMEA), where paint line characteristics for example, are measured to help improve its production processes by looking at where any failures occur to ensure the highest quality standards.
Previously, inspection and compliance audits were completed manually using check sheets that were then filed by its quality control technicians. The problem with this was that these lists could be easily misplaced or damaged as they would often be filed the next day. This meant that when it came to large external audits, it would take a couple of weeks for staff to manually check for these types of errors or the manufacturer would risk not being able to supply at all.
How Does Digitisation Deliver?
By introducing WorkfloPlus integrated with tablets its quality control technicians can easily follow digital instructions to complete quality audits and compliance tasks. The technicians are required to log when the process has been completed,by whom and upload supporting photos taken with their tablets, so the data is accurate for compliance purposes and is easily shared with key customers.
Rimstock’s technicians quickly found WorkfloPlus easy to operate for routine quality audits, simply following the instructions on the tablet to complete the audits stepby-step, it’s currently used for 15-20 workflows a week and can be easily updated as new parts come online.
Mike continues: “Our largest customers are European based, so the ability to share images of the finished product is of huge importance to us. We had been experiencing problems with one of our key customers, but once WorkfloPlus was introduced any issues dropped right off as our new automated system is so robust.
“WorkfloPlus allows us to show the engravings on individual parts and of course you can enlarge the photo for even finer detail. It also means that lots of the many smaller checks are never missed, like checking the paint film build next to the cap, it’s easy to forget unless you have digital instructions to follow.
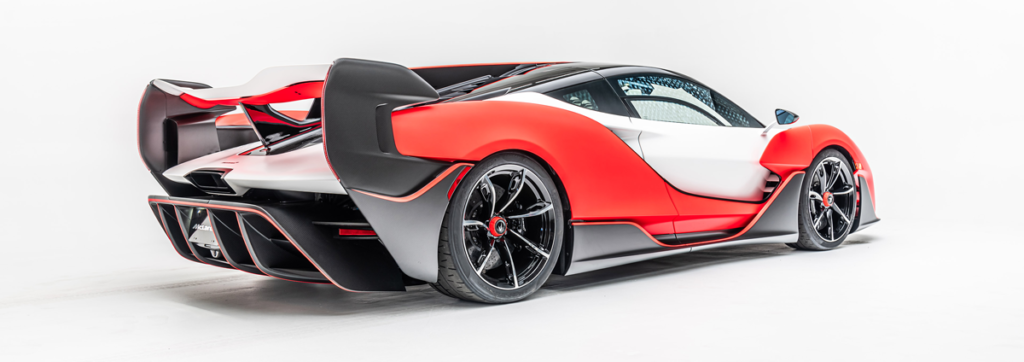
Our alloy wheels often go to third-party fitters, but we were finding two major issues; damage to the back rim of the wheel as some types of packaging can lead to scuff marks while in transit and damage from removing the wheel from its packaging. Alloy wheels typically weigh 8-9 kilos so they can be easily dropped by fitters, previously Rimstock would be held responsible for this type of damage, but with WorkfloPlus we can challenge these issues with complete confidence.”
By February 2020, Rimstock was able to get its returns in ppm down, so the impact of digitising is easily measured. WorkfloPlus had proved itself in terms of financial ROI, compliance and operational efficiencies thanks to improved quality controls and real-time data reporting. But most importantly, it helped the manufacturer improve relationships with the world’s leading OEMs it supports.
What’s the future for WorkfloPlus and Rimstock?
Rimstock has recently appointed a quality manager so we’re starting to do control plan audits, which means getting into the fine detail of how the paint facility runs and questioning everything and creating a Gap Analysis of what we need to do. The way we fill the ‘gaps’ is by using WorkfloPlus to share key data on how jobs are completed.
The next stage is to map out exactly what we need to do in the future, our workflows need to integrated with our existing ERP system to unlock further operational efficiencies beyond the paint facility to include the entire manufacturing plant – that’s the aim for the next two years.” Mike Wise, Operations Manager, Rimstock